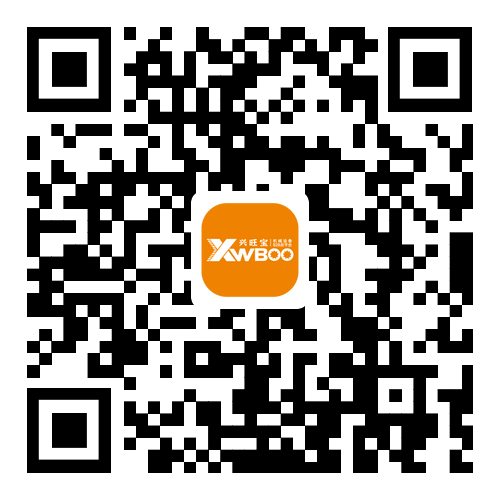
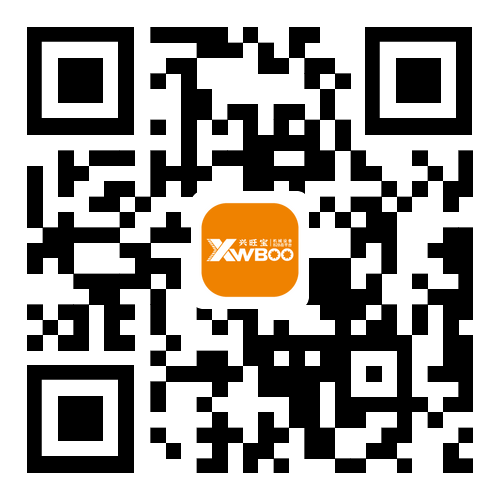
产品详情
铸铁平台的用途:铸铁平台是检验机械零件平面、平行度、直线度等形位公差的测量基准,也可用于一般零件及精密零件的划线、铆焊研磨工艺加工及测量等。铸铁平台是用于工件检测或划线的平面基准器具。铸铁平台主要用于检验工件误差的基准,铸铁平台在机械制造过程中起着至关重要的作用,它是每个工件出厂前检验的最基本基准工具。铸铁平台用途比较广泛,应用于机械制造、化工、五金、航空航天、石油、汽车制造、仪器仪表制造等行业。
铸铁平台材质:铸铁平台采用优质、细密的灰口铸铁HT250或HT200为铸造原材料,工作面硬度为HB170-240,经过两次人工热时效处理(人工退火600度-700度和自然时效2-3年)使其精度稳定,耐磨性能好,强度符合国家有关标准。
铸铁平台的设计制造要符合JB/T794—1999《铸铁平板》标准,产品制成筋板式和箱体式,铸铁平台工作面有长方形、正方形或圆形,材料HT200-300,QT400-600,ZG15-45。铸铁平台工作面采用刮研工艺,工作面上可加工V形、T形、U形槽、燕尾槽、圆孔、长孔等。
铸铁平台规格:200×200-3000×8000mm,特殊规格铸铁平台可按用户图纸订做或双方商定生产加工。
铸铁平台精度:铸铁平台按国家标准计量检定规程执行,分别为0、1、2、3四个等级。
铸铁平台技术设计要求
首先根据我公司多年的设计经验,以提高铸铁平台的质量、降低铸铁平台的成本并确保铸铁平板美观合理为设计理念,对铸铁平台进行技术设计。
1、铸铁平台的设计制造要符合JB/T794—1999《铸铁平板》标准,铸铁平台及所有附件的计量单位全部采用国际单位(SI)标准。
2、铸铁平台需进行两次人工时效处理。次时效处理在粗加工前,以消除铸造应力。第二次人工时效处理在粗加工后,以消除粗加工产生的应力。
3、全部铸铁平台的调整采用可调垫铁调整,使铸铁平台调整方便可靠且降低需方采购成本。
4、严格把关铸铁平台外观及表面质量。
5、铸铁平台无锈迹、滑痕等其他影响使用的外观缺陷,不允许有严重影响使用性能的砂眼、气孔、裂纹等铸造缺陷。 其余部分无裂纹、影响外观和使用性能的严重铸造缺陷。
6、铸铁平台加工面涂防锈油,非加工面涂防锈漆,面漆。
7、为提高铸铁平台的抗变形能力,按材料力学强度理论,采用箱型筋式结构,截面采用高强度的半封闭式箱型截面,使平台纵横剖面均呈“工”字梁结构。大大提高平台的抗弯截面模量,从设计模型上保证平台有足够的强度、刚度和稳定的精度。
8、为地减小装卸起吊平台过程中,铸铁平台自重对其精度的影响,全部铸铁平台吊装孔设计符合贝塞尔支点原理。
按照以上方面对铸铁平台的质量、成本、外观进行技术设计,如上执行标准并结合我公司多年的设计经验,完成铸铁平台的技术设计才是最合格并的设计方案。
铸铁平台的质量检验:
铸铁平台外观质量检验比较简单,检查是用肉眼或借助放大镜、管道镜级尖嘴锤等工具,观察寻找暴露早铸铁平台外表面的缺陷,如:裂纹、表面气孔和缩孔、粘砂等缺陷,利用卡尺、直尺、千分尺、样板和工作台平台,有条件的地方可利用三坐标测量仪等来检验铸铁平台尺寸是否符合图纸要求和尺寸偏差是否在允差范围内,借助各种秤量工具来检验铸铁平台质量是否在允许范围内等。
铸铁平台表面缺陷检验分为:腐蚀法检查、渗透检查、磁力探伤,利用这几种判断方法来检验铸铁平台是否表面缺陷。内部缺陷检验:①放射线探伤用于检查铸铁平台内部的气孔、缩孔、砂眼、夹渣、针孔、裂纹等缺陷。②超声波探伤利用超声波在铸铁平台中传播时遇到缺陷界面能反射这一原理来发现铸铁平台内部缺陷的。③耐压检验使用承受压力和耐渗漏的铸铁平台,一般都要进行耐压试验。为此小件可浸在水中试验,大件铸铁平台可在易产生缺陷的部位或怀疑处涂上肥皂水,当有气体渗出时,就有肥皂泡出现。理化性能检验具体的检验内容及要求取决于铸铁平台的验收条件。这样才能更好的在铸铁平台生产工艺的控制和改进,有利于提高铸铁平台的质量。
铸铁平台平面度的检验标准:铸铁平台平面度用涂色法检验。
1级铸铁平台在每边为25㎜平方的范围内不少于25点。
2级铸铁平台在每边为25㎜平方的范围内不少于20点。
3级铸铁平台在每边为25㎜平方的范围内不少于12点。
铸铁平台的日常养护:
1、为了防止铸铁平台发生的变形,在吊装铸铁平台时,要用四根同样长度的钢丝绳同时挂住铸铁平台上得四个起重孔,将铸铁平台平稳吊装在运输工具上。
2、将铸铁平台支承点垫好、垫平,保证每个支撑点受力均匀,保证整个铸铁平台平稳。
3、铸铁平台安装时,将铸铁平台的各个支撑点用调整垫铁垫好、垫实,由专业技术人员将铸铁平台调整至水平、铸铁平台使用时要轻拿轻放工件,不要在铸铁平台上挪动比较粗糙的工件,以免对铸铁平台工作面造成划伤、为了防止铸铁平台整体变形,使用完毕后,要将工件从铸铁平台上拿下来,避免工件长时间对铸铁平台重压,造成铸铁平台的变形。